row
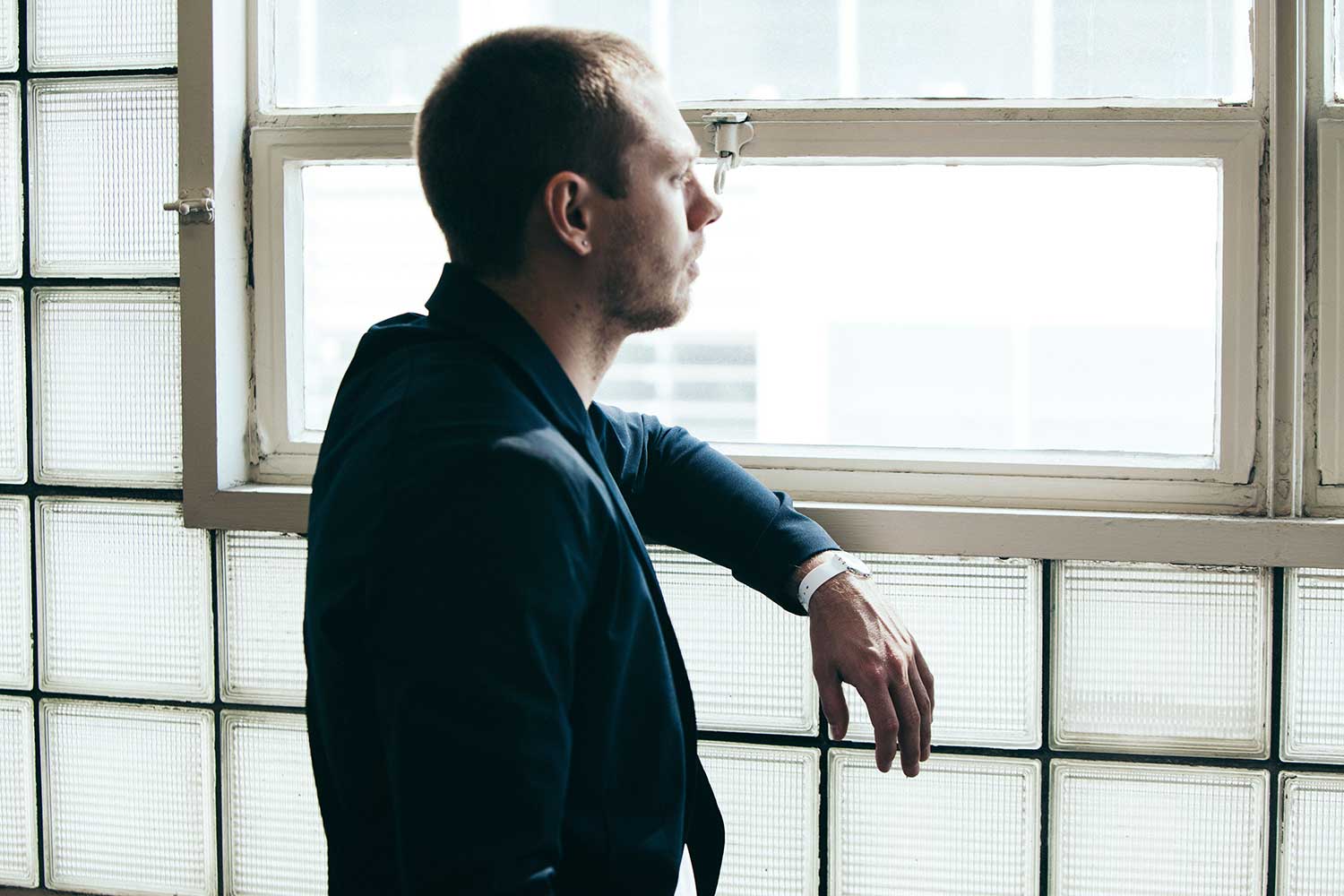
Skylar Tibbits' approach to problem-solving? Never start with an actual problem.
Skylar, a TED Fellow pioneering the field 4D printing, founded MIT's Self-Assembly Lab on the belief that if you create truly innovative platforms and tools, the applications will come naturally. This consideration of all angles – not just the intuitive – has given way to breakthroughs like 4D printing that can be translated into game-changing solutions across industries, from aeronautics to furniture (think: self-assembling chairs).
We sat down with Skylar to learn more about his invention process, current applications, and why you'll never find his team shying away from the unknown.
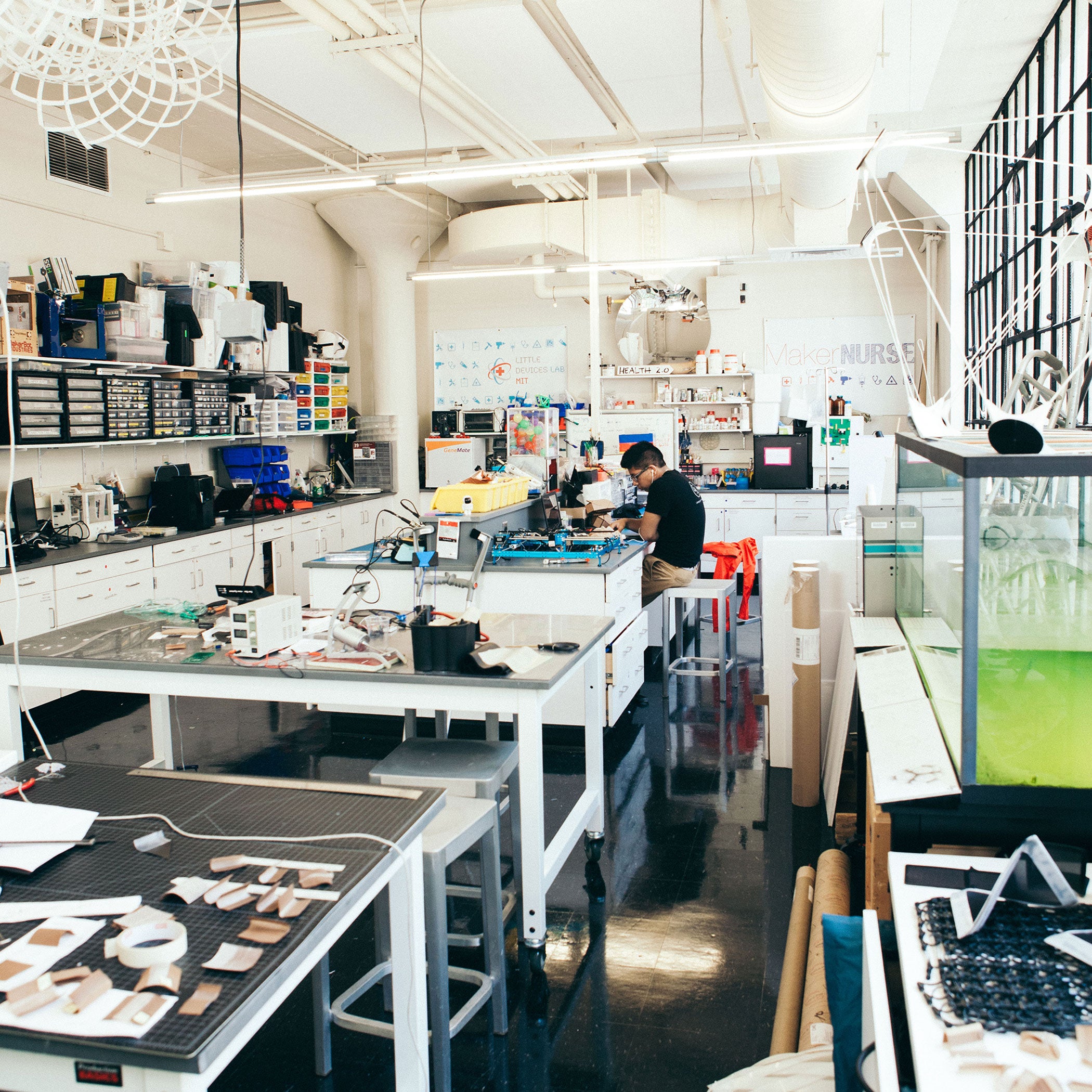
SKYLAR:
To preface this – we don’t start by trying to solve problems. I don’t ever want the lab to be driven by solving problems, because I think that only leads to incremental development. If you deliberately set out to solve a problem, then you’re considering all the other attempts that have been made to solve it, and just trying to do something a little better. Your whole world is that problem. You’d never think about coming from a totally different angle that might lead to a crazy solution, because you only know it from a micro lens.
We start by asking, “What is the best thing that we could do in general?”, separating research from application and profitability to consider the craziest thing possible. And those things tend to end up solving problems that you’d never even foresee. For example, we didn’t start with 4D printing out to solve this, this, and this. We weren’t thinking that it would be great for, say, medical devices, or shoes. We were naive about it, thinking, “Wouldn’t it be awesome if we could just print something and it could transform?” No motors. No sensors. No wires, no assembly, no nothing. Just print, activate, and then it does something amazing on its own.
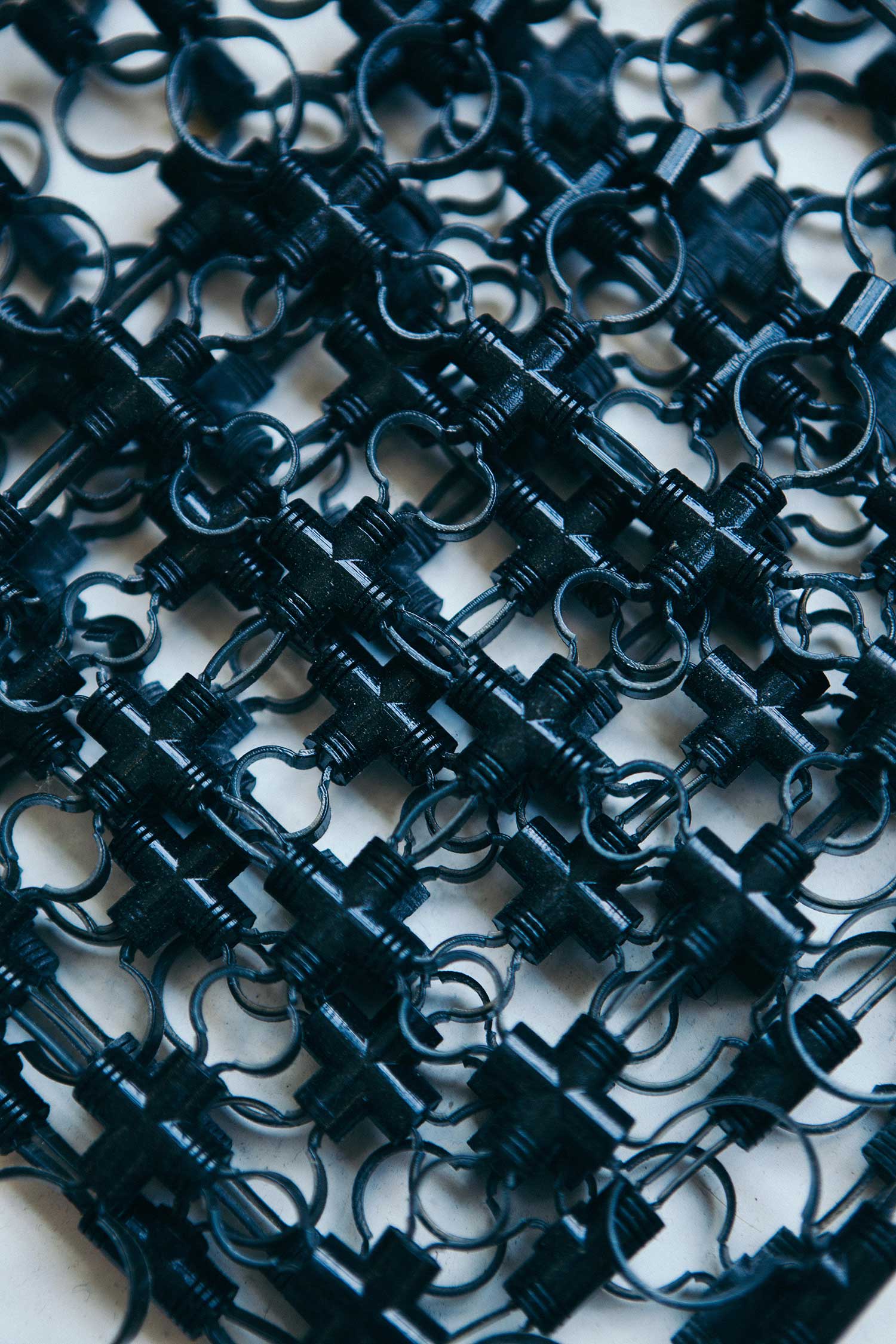
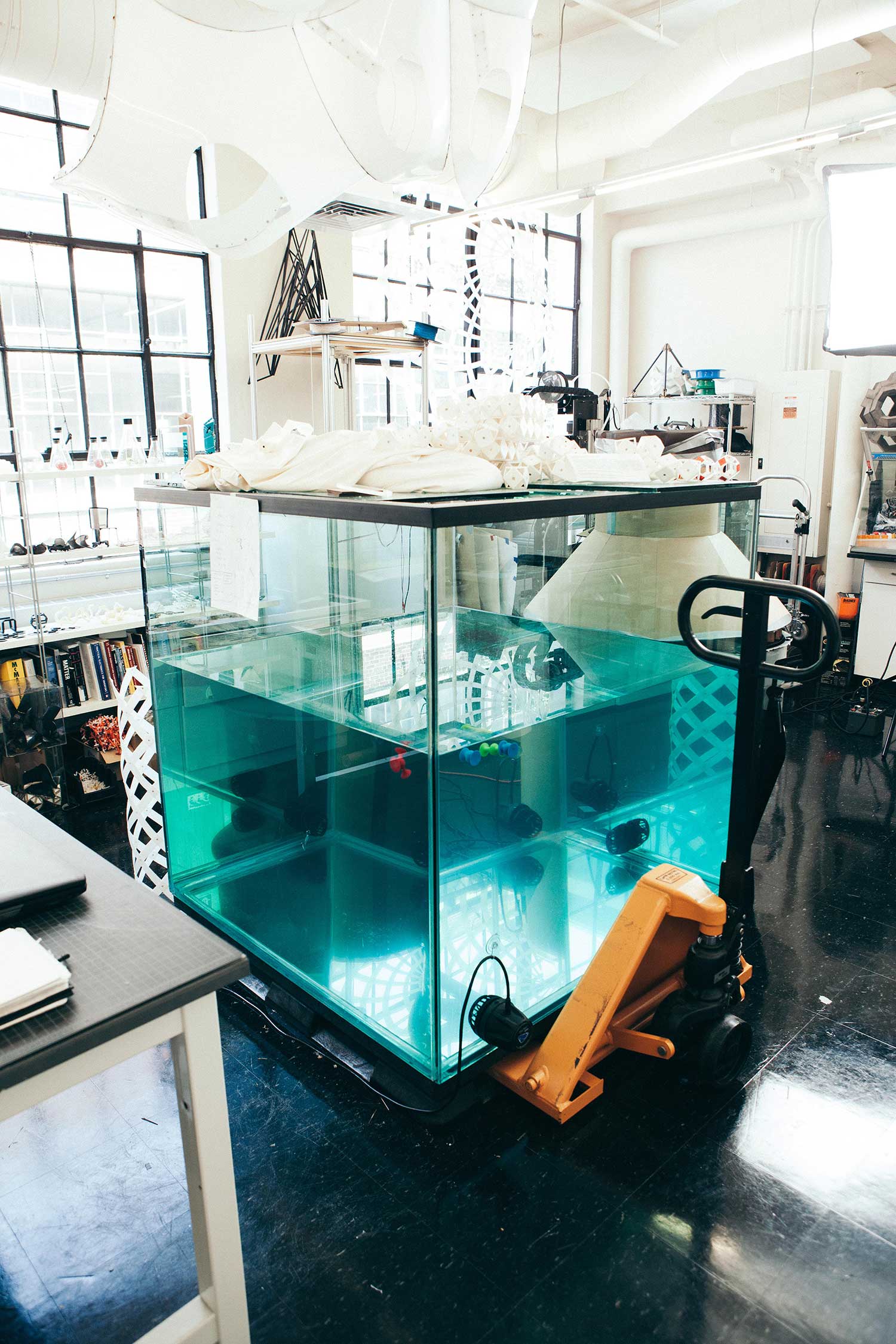
And then when we started doing that, lots of people came to us asking if we could do 4D printing for things like cars, clothing, and so on. The applications find you. None of them are perfect, but you always realize, “Oh, that’s a good idea – you could then tweak it this way, and maybe it could solve XYZ…” So then it’s more about trying to apply it. And a lot of innovation has to happen to apply it to this spectrum.
The most exciting approach for us isn’t so much this little thing we have to solve, but identifying a challenge in an industry and asking, “What are totally different ways to think about this challenge?” Because now we’re thinking about these challenges in the context of a new technology - like 4D printing or programmable materials. I think that leads to big leaps instead of incremental developments.
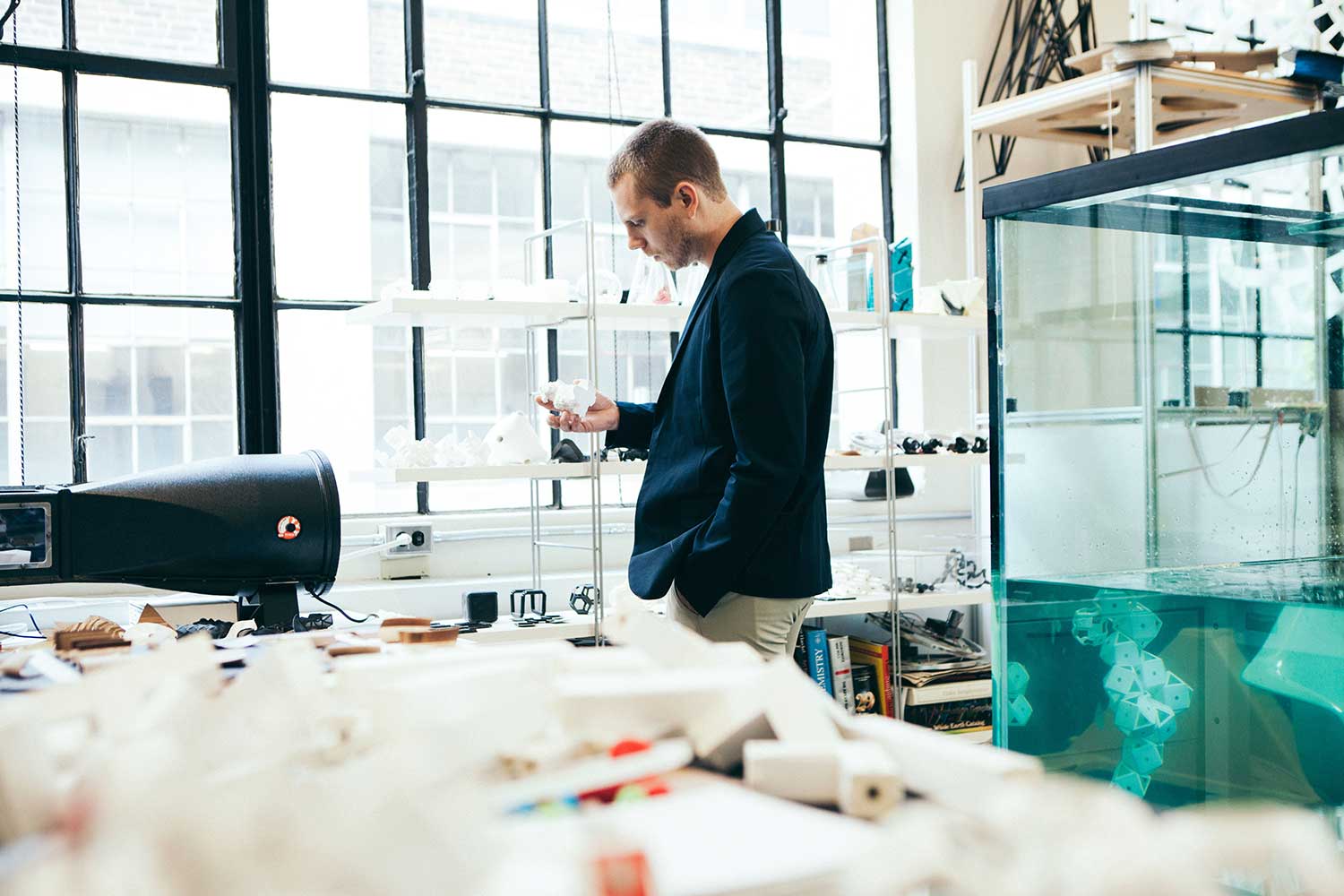
We’re working on a number of specific projects right now – for example, components that regulate cooling in an airplane engine. The conventional solution would be mechanical flaps; but because we have this new technology, you can converge two different worlds and to bring about this material that morphs itself to control the airflow. We’re also looking at morphical structures for support and movement and compression within medical devices, plus new capabilities for composite materials. And then there are a lot of very specific technical considerations: how do we scale up on a lot of these things, how do we translate them into more industrial production, how do we work with a very specific material like rubbers or wood, and then how do we make new machines to do these things. It all comes with a lot of challenges.
Shop